
Title
Why
When a procedure is performed, internal quality controls need to be performed to know that each step of the procedure is done properly and that the output of that procedure is quality controlled.
What
For each procedure in the laboratory internal quality controls must be formulated. This should be done using the flow charts developed in the previous activity. For each process step in each flow chart one should think of what can go wrong. Internal quality controls must then be developed to make it possible to detect when something goes wrong. This makes the process step quality controlled. To make a complete procedure quality controlled, as many internal quality controls as necessary should be included.
Per procedure performed in the laboratory the internal quality controls must be listed. This means not only the examination procedures. Also preparation of reagents, preparation of media, checking correct transcription of results on Result Reports, etc. need quality control steps. The results of internal quality controls must be archived. These records need to be used for periodical review of quality control results.
In the WHO Laboratory Quality Management System (LQMS) handbook a lot of information is provided on quality control; see the documents in the right-hand column.
How & who
Quality Officer in combination with laboratory staff involved in the different procedures:
- See the images below:
- Use the flowcharts developed in the previous activity: determine for each process step things that can go wrong (and write these down next to the process step).
- Formulate for each possible failure a quality control step that enables you to detect when the failure occurs. Below is an illustration in which this, and the previous step were done for two steps of the process of analyzing Gram stains.
- List for each procedure which internal quality controls should be established and determine also the frequency with which these controls should be done (e.g. "Daily", "Weekly", "With each new batch", etc.).
- The specific protocol for performing internal quality controls varies per procedure. Therefore the protocol for performing the quality controls must be included in the SOPs for each procedure. I.e. quality control must become an integral element of all the procedures performed in the laboratory. If SOPs for certain procedures have already been developed, adapt these SOPs to include the quality control protocols and forms. If SOPs for certain procedures have not yet been developed: later in this phase SOPs need to be developed for all procedures routinely performed in the laboratory.
- Adapt the result registers to include room for inserting quality control data.
- Write an SOP for Internal Quality Control according to the protocol for writing a Procedure SOP in the Master SOP and use the template for a Procedure SOP attached to the Master SOP. In the SOP for Internal Quality Control the general procedure for performing an internal quality control needs to be described. Include in this SOP the following elements:
- Explanation on the concept of internal quality control; what it is and why it must be done.
- The general procedure for performing an internal quality control and explain that the internal quality control data must be recorded in the laboratory register. This makes verification of execution of quality controls possible and also enables the laboratory to monitor trends in quality control (see below).
- Procedure for developing internal quality control materials: these should imitate patient materials as much as possible. Also explain which control steps must be taken to ensure that these materials are of good quality. Refer to SOPs of specific laboratory procedures for protocols on developing specific internal quality control materials for a certain test or procedure.
- The procedure for periodic review of internal quality control data to detect trends in performance of internal quality controls that could indicate problems in examinations. Use statistical techniques for continuous monitoring of internal quality controls. See for further information the next activity.
- The procedure that should be followed when an internal quality control fails (meaning that the process step covered with that quality control is not performing properly and the quality of the output/result of the whole procedure is compromised). It may never happen that examination results are reported in case of quality control failure! See also next point
- Develop a nonconformity form. On this form the quality control failures must be recorded. This will be needed later in phase 3 when quarterly reports and management reviews will need to be produced. In the right-hand column a template for such a form is provided. Store completed forms in a new folder titled “Nonconformities”.
- Include the SOP in a Read and Understand List and indicate which staff members have to read the SOP (those for whom the SOP is relevant for their work).
- Present the concept of internal quality control and the SOP for Internal Quality Control in a weekly staff meeting and explain all the above mentioned elements of the SOP. Explain who should do which quality control and at which time. Indicate which staff members have to read the SOP and explain that they have to sign the Read and Understand List when they have read the SOP.
- Start the use of internal quality controls as described in the SOP for Internal Quality Control.
- In the early stages: check if internal quality controls are done correctly and according to schedule. If not: track down the problem. E.g. if it is a staff member that doesn't understand how internal quality control needs to be performed for a certain test, explain the procedure to him/her again.
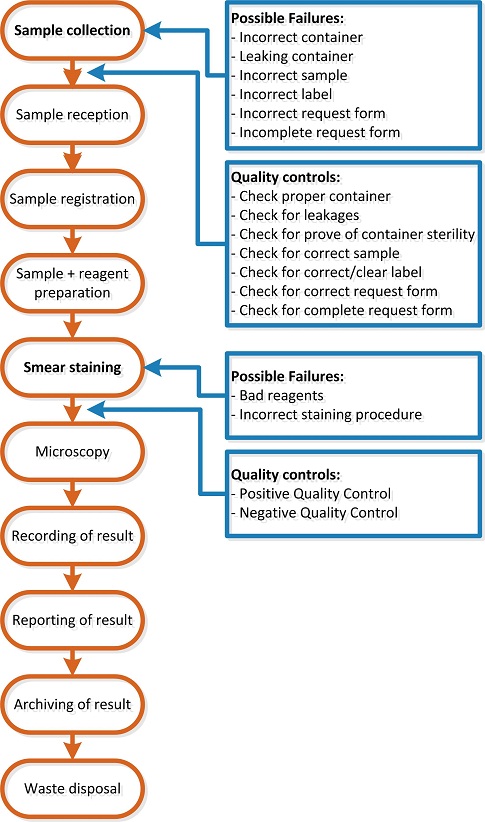