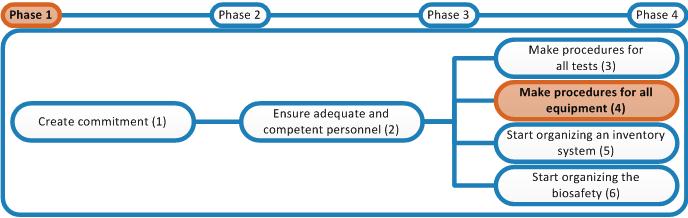
Title
Why
Making an overview of which equipment is present in the laboratory is the first step in implementing a quality management system for equipment. The equipment register contains specific details about each piece of equipment (such as maintenance and calibration dates, maintenance frequency, who is responsible for the equipment, etc.). Hence, the equipment register is the most important element in managing the quality of equipment.
When the equipment register is made directly check the functioning of each piece of equipment and record this in the equipment register so that it is clear which pieces of equipment have priority in planning for maintenance (which is part of phase 2 of this tool).
What
Create an Equipment Register. This is an overview of all equipment present in the laboratory including the most important details. In phase 2 a file will be made for each piece of equipment that will contain more elaborate information.
Record the following details of each piece of equipment:
- Identity
The name of the piece of equipment, including its type/model where applicable - Label
Make this yourself: use a logical label that includes the abbreviated name of the laboratory (to indicate that the equipment is owned by the laboratory) and a unique code for the piece of equipment - Serial number
This is a number provided by the manufacturer - Manufacturer name
- Manufacturer's contact person and contact details
- Date of purchasing
- Date of putting into service
- Location
E.g. room number and, if applicable the building number - Condition
E.g. "Functioning properly"/ "In need of calibration"/ "In need of maintenance"/ "Defect" - Service provider name
- Service provider's contact person and contact details
- Frequency of maintenance
How often per year is maintenance and calibration needed? - Date of previous maintenance
- Date of next scheduled maintenance
- Remarks
Additional information, if needed.
In the right-hand column a template equipment register is provided.
How & who
Equipment Officer:
- Make an inventory of equipment present in the laboratory. You can do this on paper or digitally if possible. It is more convenient to make a digital register as this poses less work when adaptions need to be made. Be sure to include all the details listed above. In the right-hand column a template Equipment Register is provided that includes the above listed details.
- Be sure to include all equipment. Think of computers, autoclaves, incubators, centrifuges, laminar flow cabinets, pipettes, timer clocks, etc.
- Determine for each piece of equipment if it is functioning properly for the examinations performed. Also ask the staff members using the piece of equipment frequently whether it functions properly.
- If you have identified a nonfunctional piece of equipment and this piece of equipment has a direct critical effect on laboratory testing, put it out of service, determine which repair must be performed, and explain this to the laboratory manager. Critical means that the absence of a properly functioning piece of equipment makes specific routine laboratory examinations impossible to be performed.
- Determine if there is a critical need for a specific piece of equipment that is not present in the laboratory at this moment.
- If this is the case, list the characteristics of the piece of equipment needed and submit this to the Laboratory Manager.
Laboratory Manager:
- When the Equipment Officer indicates that specific pieces of equipment need repair, identify funding and arrange repair. If extensive repairs are needed to a certain piece of equipment, determine whether it is more cost efficient to purchase a new piece of equipment or to go on with repairing the old piece of equipment.
- The Equipment Officer also drafts a list with new equipment needed to enable correct performance of laboratory examinations. Investigate the procurement options for each piece of equipment and determine the amount of funding needed. In choosing the equipment take into account:
- That reagents are available and easily deliverable.
- That specific technical maintenance must be possible (e.g. a maintenance company is available that is capable of performing specified technical maintenance on the equipment, or that training can be given in the laboratory by the company that installs the piece of equipment, in order to learn how to perform maintenance on the equipment).
- Identify the funding and purchase the required equipment.