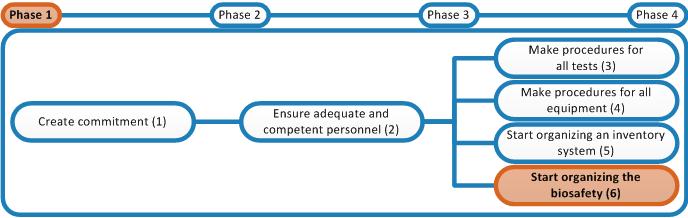
Title
Why
It is difficult, if not impossible, to provide a stepwise plan in this tool for upgrading the facilities and safety that is relevant to every laboratory. As the state of the facilities and safety can differ greatly between laboratories, it is impossible to present one unified approach that will work for all laboratories. Therefore this tool uses another strategy to help improve facilities and safety.
What
First the biosafety level needs to be determined for every room of the laboratory building, which depends on the type of pathogens worked with in the laboratory. The biosafety level determines which safety requirements the laboratory should adhere to. These can be found in ISO 15190:2003 'Medical Laboratories - Requirements for Safety' and the World Health Organization (WHO) Laboratory Biosafety Manual. [TB] For more TB specific information please refer to the Tuberculosis laboratory Biosafety Manual. The Biosafety Officer should develop an action plan so that the laboratory comes into compliance with these requirements.
A second strategy, aimed at putting into place the basic safety measures applicable to all types of laboratories, is conducting a biosafety assessment, which will be done in the next activity. The non-compliances found in this assessment need to be translated into action points which are also included in an action plan.
Another useful reference document for biorisk management is the CEN Workshop Agreement 15793 Laboratory Biorisk Management. This CWA is based on a management system approach and implies that identifying, understanding and managing a system of interrelated processes for a given objective will lead to improvements in the organizations' effectiveness and efficiency.
How & who
Biosafety Officer:
- This tool follows the principles as described in ISO 15190:2003 Medical Laboratories - Requirements for Safety. It is therefore recommended to refer to this standard.
- In ISO 15190 (paragraph 4) and chapter 3, 4 and 5 of the WHO Biosafety Manual the different Risk Groups are explained. Determine in which Risk Group every room of the laboratory falls based on the examinations being performed and the pathogens worked with.
- Determine for each laboratory room and for the laboratory as a whole which improvements are necessary to comply with the requirements of the specific Risk Group.
- Translate the points for improvement into action points and define who should do each action point and at which moment they should be completed. Remember to adhere to the SMART principles!
- Include all action points into one action plan titled: "Facility and Safety Risk Group Improvement Plan".
- Check timely and correct implementation of action points. If completion of certain action points is not yet done after passing of the deadline, notify the Laboratory Manager who has to ensure that the assigned person implements the action point as soon as possible.
Laboratory Manager:
- Schedule meetings with the Biosafety Officer once per two weeks to discuss the improvement process of the facilities and safety and check the completion of action points.
- If the Biosafety Officer indicates that certain action points are not yet implemented while their deadline has already passed, make the assigned staff member complete the action point as soon as possible. Provide assistance and further clarification for the staff member when needed.
NOTE that it is not required to comply with all the safety requirements already at the end of phase one. It is important that the laboratory complies with the requirements when accreditation is requested.