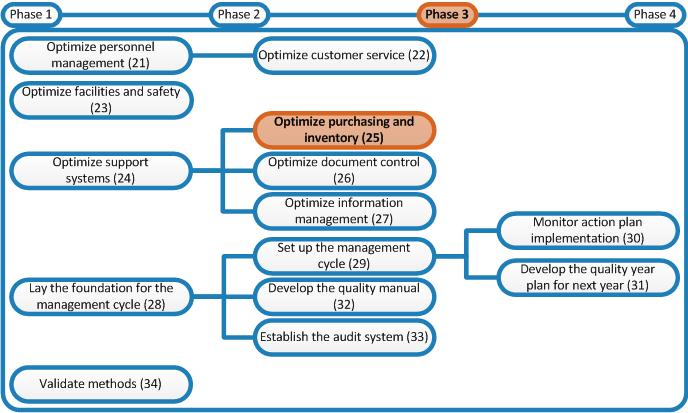
Title
Why
Budgeting for purchasing and maintenance of equipment must be done to be better able to finance this when this is needed.
What
Equipment depreciation:
- Write down for each piece of equipment:
- The estimated costs per year for maintenance of the piece of equipment.
- The estimated date on which the piece of equipment will have to be replaced because it is getting too old.
- The estimated price of a new piece of equipment replacing the old one.
- Divide the price of a new piece of equipment that will replace the old one over the number of years remaining between now and the expected replacement date. This is the equipment depreciation cost for this piece of equipment.
- Calculate the amount of money that should be set aside each year for the piece of equipment by adding the yearly equipment depreciation cost to the yearly costs for equipment maintenance.
- Do this for each piece of equipment present in the laboratory.
- Calculate the sum of yearly equipment depreciation costs for all equipment present in the laboratory. Include these costs in the budget for the next year under the expense "Equipment depreciation".
- Calculate the sum of yearly maintenance costs for all equipment present in the laboratory. Include these costs in the budget for the next year under the expense "Equipment preventive maintenance".
- Make an estimation of the yearly costs of equipment repair; as repair is often unexpected it is not possible to know the exact amount of money needed for the next year. However, try to make a rough estimation of the average amount of money spent on equipment repair over the last years and include this amount in the budget for next year under the expense "Expected equipment repair".
In many countries laboratories cannot have a depreciation system and due to the financing system. In this case the laboratory has to think of an alternative system for ensuring continuity of the laboratory (i.e. preventing that examinations cannot be done due to break down of old equipment). E.g. try to anticipate break down of old equipment by identifying which pieces of equipment will not last long anymore and start to look for funding to have replacements ready before these pieces of equipment break down.
New equipment:
- When making the yearly budget, see if you will need to buy new equipment next year, e.g. in case you want to include new examinations in the laboratory routine testing that are not yet performed at this moment.
- Include the estimated price for this equipment in the budget, taking into account shipping and installation costs (under the expense "New equipment purchases").
Include also an expense for unexpected equipment repairs when equipment breaks down. Determine what is a reasonable amount of money so that for the average equipment repair there is always enough money available.
How & who
Laboratory Manager:
- Perform the above mentioned steps. Ask the Equipment Officer to assist you as he/she knows exactly which equipment is present in the laboratory, can estimate how long each piece of equipment will last, and can indicate how much maintenance must be performed on each piece of equipment every year.
- Do this every year when making the budget for the next year.