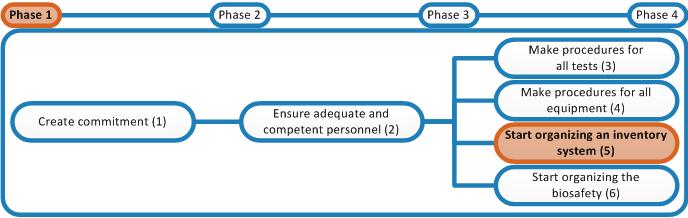
Title
Why
To know which supplies and how much of each supply is available in the laboratory stock, an inventory register needs to be made. This is a database with records containing details of all the available supplies. The first step in making the system inventory register is the design and use of Stock Cards (on paper or electronically).
What
Design the layout of a Stock Card. The Stock Card should leave room to fill out the following details:
- Name of the item in stock
- Date and amount ordered
- Date of receipt of item
- Amount received
- Lot-number
- Expiry date
- Date the material was placed in service
- Amount of items used
- Balance of items in stock (number still in stock)
The Stock Cards can either be maintained in an electronic database (Excel or a dedicated program) or in a paper database. A template stock card in MS. Word (for a paper system) is provided in the right-hand column. [TB] In the same column you will find a tool and an example more specific to TB laboratories.
How & who
Stock Officer:
- Design the Stock Card. The Template Stock Card provided in the right-hand column could be used as a start.
- If on paper: Print a sufficient number of Stock Cards (of each item in the stock a Stock Card should be filled-out).
- Take a new folder and title this "Stock Inventory Register". Place two tabs in this folder, one named "Orders" and one named "Stock Inventory". Order forms of orders that have not yet been received by the laboratory are placed behind the "Orders"-tab and the Stock Cards with details of all items already in stock are placed behind the "Stock Inventory"-tab. If an electronic register is used: create a similar system that helps you to keep track of which items are ordered and which are already in stock (and in which quantity).
- Fill-out a Stock Card for each item in stock.
- If necessary, make a good system for orderly division of items in stock. E.g. place items in alphabetical order of names and place the oldest item in the front and the newer items in the back so that the older items are used first, decreasing the risk of using expired products.
- Present to all staff members in a weekly staff meeting how the stock inventory system works and what a Stock Card is. The laboratory manager will explain that nobody is authorized any longer to take items from stock and that they have to ask you if they need something. This way you can keep the Stock Cards up to date and prevent differences between the quantities in the stock register and the actual stock as much as possible. Note that you always have to help colleagues who need something from the stock directly.
- Perform a stock balance once per quarter: count of each item how many there are in stock, and see if this is in accordance with the amount indicated on the Stock Card. If not, update the Stock Card. Also check expiration dates and discard items that are expired. [TB] On the right you will find an example how to calculate monthly consumption together with a sample of a quaterly control stock card.
Laboratory Manager:
- Stress during the weekly staff meeting in which the Stock Officer presents how the stock inventory system works that the Stock Officer is now the only person that is allowed to take items from the stock. This way the Stock Officer can update the Stock Cards directly and it is prevented that quantities in stock start to differ from quantities in the register. Explain also that each newly arrived order must be inspected and unpacked by the Stock Officer. Nobody is allowed to place items in the stock him/herself as the laboratory must segregate uninspected/unaccepted supplies from inspected/accepted supplies.
- Adapt the Authorization Matrix to specify that nobody is authorized to take items from stock except for the Stock Officer.