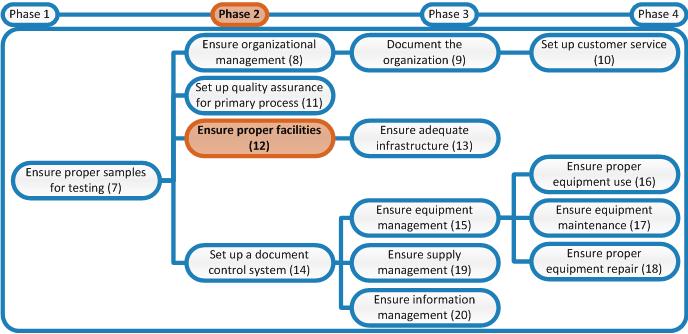
Title
Why
Often the different procedures performed in the laboratory can negatively affect each other. For example: molecular techniques such as PCR should be done in another room than culture. If conducted in the same room culture could contaminate PCR samples and cause false positive results. Areas should be separated if conflicting activities are performed.
It is also important that the laboratory floor plan is logical. When staff have to walk a lot through the laboratory the work efficiency decreases and the risk of bumping into each other and potentially causing a spill is increased. Also, the most dangerous activities (such as drug resistance culture) should be performed in an area where the least people come, for example at the end of the corridor.
Thirdly, adequate staff facilities should be in place: staff should have a room separate from the laboratory where they can have breaks, they should have adequate office space to do paper work, wash rooms should be available and storage space for clothing, handbags and personal protective equipment. It is also important to have a safe supply of drinking water.
What
Separation of processing areas:
- The primary sample collection area should be separated from the laboratory.
It must be ensured that this area allows proper sample collection without risk of infecting the patients (having an already weakened immune system, they are extra sensitive to the pathogens present in the laboratory). Include patient comfort in designing this area (e.g. patients should be able to sit comfortably, protected from direct sunlight and rain, in a well-ventilated area). In phase 3 more attention is paid to design of primary sample collection areas. - Culture is performed in a separate room. Drug resistance culture may be separate from initial culture.
If necessary with negative pressure if worked with biosafety class III pathogens. - A unidirectional workflow is in place for molecular work to prevent cross contamination
E.g. in the PCR laboratory an entry door and an exit door must be used and different areas are available for different steps in the process. - There is a separate room for cleaning of laboratory glassware and autoclaving waste and glassware.
Floor plan optimization:
- Redesign the floor plan to increase work efficiency and create a unidirectional workflow where possible. Read the WHO Laboratory Quality Management System (LQMS) Information Sheet on Laboratory Design provided in the right-hand column. [TB] For TB specific floor design see the appendix 12 of Priorities for TB bacteriologiy services in low-resource countries and the section 2.3 of the TB laboratory biosafety manual in the right-hand colunm.
- Create an office area separate from laboratory rooms with adequate office furniture.
- Create a room where staff can have breaks/lunch (not in laboratory rooms!).
- Ensure supply of drinking water.
- Create locked storage areas for clothing, personal items and personal protective equipment.
- Ensure adequate ventilation and lighting in all rooms.
See ISO 15190:2003, paragraph 6.3, for all the requirements for conditions in the laboratory facilities.
How & who
Laboratory manager:
- Make a list of all the measures that should be taken to prevent cross contamination and unsafe situations. Ask for clarification from the Biosafety Officer if anything related to biosafety is unclear.
- Make a new, optimized laboratory floor plan using the WHO LQMS Information Sheet on Laboratory Design.
- Make a list of action points needed to create the new laboratory floor plan (take the above mentioned requirements into account).
- Make a planning of when which measure of both the floor plan optimization and processing area separation should be completed and by whom.
- Translate these measures into SMART action points.
- Include these points in an action plan entitled "Upgrading of Laboratory Floor Plan".
- Monthly check if action points are completed in time and correctly. If not, take appropriate actions to complete delayed of incorrectly completed action points as soon as possible.
Biosafety Officer:
- Assist the Laboratory Manager in this activity if asked.