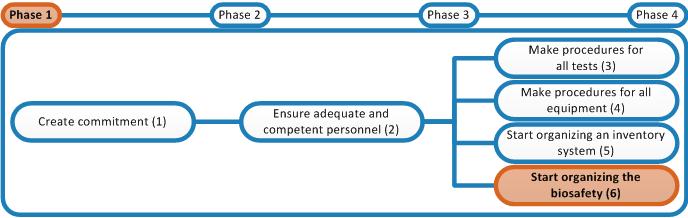
Title
Why
The laboratory must be clean and tidy. This decreases the risk of accidents and laboratory associated infections. Moreover, a clean environment also decreases the risk of negative influences on sensitive examinations (such as culture or PCR) through contamination.
What
Set up a cleaning schedule. The laboratory building must be regularly cleaned by dedicated and trained cleaning staff. However, the laboratory rooms themselves must be cleaned by laboratory technologists as they are familiar with the risks of the laboratory and safety procedures.
See for all the requirements to good housekeeping ISO 15190:2003 Medical Laboratories – Requirements for Safety article 13.
How & who
Laboratory manager:
- Set up a cleaning schedule that indicates:
- When which part of the building should be cleaned.
- What should be cleaned (and tidied-up)
- Include a column in the schedule that cleaning personnel have to date and sign when they have cleaned.
A template Cleaning Log Sheet is added to the right-hand column.
- Write an SOP for Cleaning of the Laboratory and include a section with specific guidelines for cleaning laboratory rooms. Write this SOP in accordance with the protocol for writing a Procedure SOP in the Master SOP and use the template for a Procedure SOP attached to the Master SOP. You will find two examples of SOPs on the right of this page.
- Add the procedure to the Biosafety Manual (i.e. cleaning is a preventive safety measure).
- Familiarize staff with this procedure; all staff members have to read the procedure and sign and date the Read and Understand List of the Biosafety Manual.
Biosafety Officer:
- Regularly check if the scheduled cleaning is consistently being done (is the schedule dated and signed for every planned cleaning, is the building indeed clean?). If not, notify the Laboratory Manager.